Reshoring is back on the agenda!
19th March 2024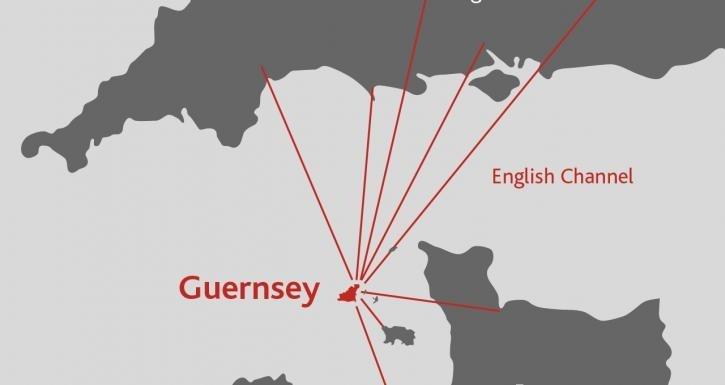
Electronics manufacturing in the far east is highly concentrated and efficient. This has allowed OEMs across the world to drive down production costs, with some partnering factories able to source components, assemble a product and ship in as little as a few weeks.
But part of what makes this approach so effective has been disrupted in recent months and there’s no guarantee normal service will resume. This has naturally led some to consider bringing their manufacturing ‘home’ or, at least, closer.
It’s always been a debate in manufacturing but reshoring is especially topical at the moment. As thisBBC article points out, some firms have now decided to permanently move production back to the UK, seeing six-figure returns as a result.
But what are reshoring’s three biggest benefits from a production point of view?
1. Control
Recent disruption has forced businesses to look beyond the balance sheet and assess the ‘full cost’ of production door to door – a move that directly supports the case for moving manufacturing closer to the point of demand. CEMs working on behalf of a client may still have to source their parts from overseas but, providing they have effective inventory management, will usually fulfil orders more efficiently than those based further afield.
For some this point is persuasive enough, but there are other key points influencing OEMs’ decision to reshore, particularly when it comes to PCB assembly. Arguably the most important factor is the greater control businesses and their subcontractors have when all operations are domestic. Offshore Electronics, for example, has used its in-house knowledge to source credible alternative parts for customers, circumventing the long lead times that have put even household brands on pause for much of the last three years.
2. Consistency
Quality control is another area where reshoring can pay dividends. Many far east facilities boast a high standard of workmanship, but it’s not always guaranteed. Domestic suppliers, on the other hand, tend to work with vetted factories that must meet minimum QC and workplace standards before pitching for tenders. Offshore Electronics’ approach offers a good case in point, with the company only sourcing PCBs and components, favoring a network of approved factories that comply with ISO 26000, ISO 16001 and ISO 14001
These points demonstrate some of the basic advantages of reshoring, though they still overlook the inherent risks associated with manufacturing across long distances in a post-pandemic market. Air and sea freight, for instance, are now significantly more expensive when compared to 2019 and the volatility around raw materials shows no sign of abating. It’s now clear the cheaper option isn’t always best for PCB design and assembly – especially in a market defined by uncertainty.
3. Clarity
Reshoring reduces the size of a company’s supply chain and the risks that come with cross-border operations. But reshoring – and even ‘nearshoring’ – is not just about the flow of goods. It’s also about communication. Electronics manufacturing is not always straightforward and certain designs will often need to be reconsidered at a later date.
This emphasizes the need for a good level of understanding between those developing a product and those responsible for building it. But this process is tricky over large distances, different languages and time zones. Closing the distance makes it easier to design and build a new iteration of a product, ultimately allowing it to reach market in a shorter space of time.
Need support with your PCB design and production? Drop us a message to find out more about Offshore’s dedicated manufacturing site in Guernsey.