Why is PCBA testing important?
13th December 2019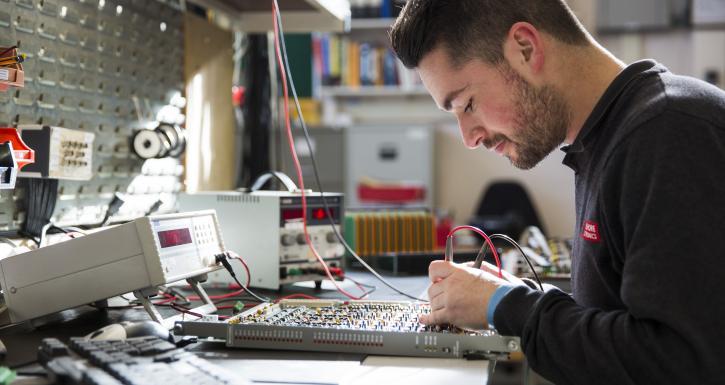
It is tempting to regard the testing of printed circuit board assemblies (PCBAs) as a necessary evil, but when done correctly, the process can add real value to your end-products. In our previous blogs, we have outlined a couple of the more common testing methods available to manufacturers and we drew comparisons between them, but why do we feel that PCBA testing is so vital?
Ensuring quality
First, you can’t guarantee the quality of your product without testing. Second, when done correctly, testing can save you time and money in the long term.
If your testing procedures are inadequate, there is a risk that you could be shipping products of inferior quality to your customers, which might lead to:
- Warranty repairs and field failures,
- Damage to your reputation,
- Could even incite lawsuits.
These issues are all sure to impact your bottom line.
Weighing the options
So then, what options are available to you for PCBA testing?
No single testing system for PCBAs will meet the requirements of every manufacturing run, and many factors need to be taken into consideration when developing a testing strategy. It is essential to select proper test procedures from the perspective of the product, business case and reliability.
The first step in building any testing strategy involves the building of a thorough understanding of the testing methods available, and to determine which of these is most appropriate for your product.
Preferred methods
At Offshore Electronics, our preferred options are automatic optical inspection (AOI) followed by functional testing and in-circuit testing. Each serves a particular purpose during the manufacture of PCBAs and it is important to understand the differences between them if effective quality control procedures are to be implemented. Automatic optical inspection checks each component is correctly placed and soldered.
As its name implies, functional testing is used to ensure that PCBAs function as they should. By contrast, in-circuit testing is used to examine each individual component on a PCBA to prove that it is correct, has been fitted to the board in the manner specified and that it works as it should. As we can already see, there are significant differences between the two testing methods.
Although in-circuit testing can include a degree of functional testing, its primary purpose is to validate each component. In some respects, it is a far more comprehensive process as components are tested independently against a program model containing parameters specific to the component and its functionality.
In-circuit testing is performed using automatic test equipment (ATE), which requires a bed of nails fixture to be built for each project. While this adds cost to the test process, it can usually be justified if the product volumes are high enough. The test program is written by our engineers, designed around the specification for the board design. In-circuit testing is also generally very fast, typically just a few seconds for even a complex PCBA, which results in a lower cost per PCBA tested.
Where in-circuit testing is not cost-efficient, functional testing can be used to examine the complete, finished assembly. Through the process, inputs and power are applied to the PCBA to ensure that it performs its desired function to a certain specification.
Normally, however, a functional test only proves that the assembly operates and does not usually detect the presence of faults in parts used as protection elements, which are inactive under normal operating conditions. Furthermore, should a PCBA fail a functional test, skilled analysis will be required to identify the root causes.
Here at Offshore Electronics, our expert production and test engineers work closely with our customers to determine the most efficient and cost-effective method of validating and testing their PCBAs to their required specifications.
Learn more with our insightful guide below or contact the team today.